Bosch Boost Compensator Operation
Basically, the boost compensator ensures that the amount of injected fuel is in direct proportion to the quantity of air within the engine cylinder to sustain correct combustion of the fuel and therefore increase the horsepower of the engine. With the engine running, pressurized air from the cold end of the turbocharger passes through the (Figure 19-63b) connecting tube from the engine air inlet manifold to the boost compensator chamber. Inside this chamber is a diaphragm (Figure 19-63a) which is connected to a pushrod, which is in turn coupled to the compensator lever. Movement of the diaphragm is opposed by a spring, therefore for any movement to take place at the linkage,
the air pressure on the diaphragm must be higher than spring tension. As the engine rpm and load increase and the air pressure within the connecting tube becomes high enough to overcome the tension of the diaphragm spring, the diaphragm and pushrod will be pushed down.
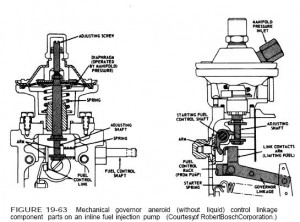
This movement causes the compensator lever to pivot, forcing the fuel control rack toward an increased fuel position. The boost compensator will therefore react to engine inlet manifold air pressure regardless of the action of the governor. When the turbocharger boost air pressure reaches its maximum, the quantity of additional fuel injected will be equal to the stroke of the aneroid boost compensator linkage, in addition to the normal full-load injection amount that is determined by the governor full-load stop bolt.
|