The smaller the nozzle orifice, the finer the fuel spray and, all things equal, the less ignition lag. But if too small, the orifice limits engine output by restricting fuel flow. Multi-hole nozzles, some with a dozen or more, electrically discharge, machined orifices that satisfy both flow rate and atomization requirements, have become standard on DI engines.
IDI engines employ pintle nozzles, two varieties of which are illustrated in Fig. 5-22. The pintle is an extension of the needle that, when retracted, produces a hollow, coneshaped spray. Because of the large diameter of the orifice and the shuttle action of the pintle, these nozzles are less susceptible to carbon buildup than multi-hole types.
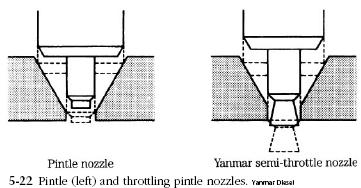
pintle nozzles Diesel Engine Fuel Injectors
The throttling pintle introduces fuel in a staged sequence to reduce the sudden rise in pressure and heat during initial combustion. The pintle has a reduced diameter on the tip that, when seated, extends into the combustion chamber. Yanmar and most other manufacturers use a throttling pintle with the tip in the form of an inverted cone, shown on the right in Fig. 5-22. During the initial phase of injection, the cone lifts so that its base almost fills the orifice. At full lift the cone retracts clear of the orifice for maximum fuel delivery. |